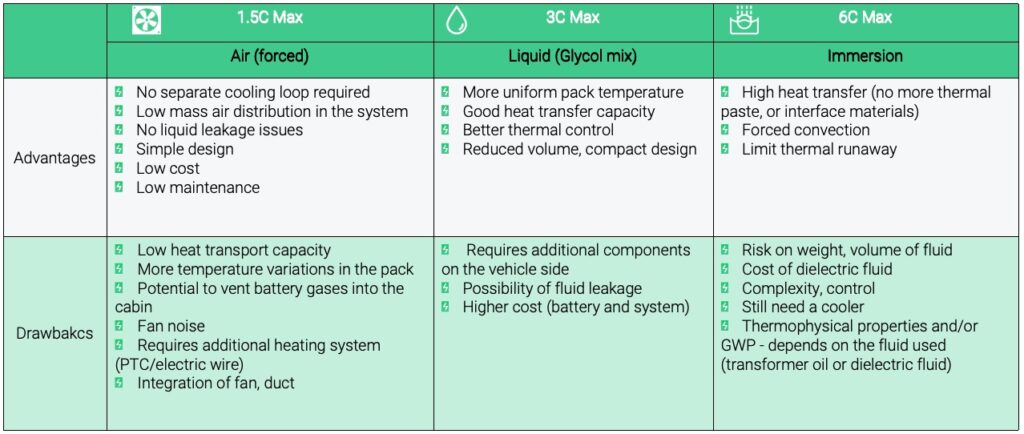
As applications become more powerful and more prevalent, managing battery temperature is no longer a design afterthought, it’s a critical system-level priority. Thermal management plays a key role in ensuring battery safety, performance, lifespan and charging efficiency.
But how do we choose the right cooling strategy? From simple air-based systems to advanced immersion techniques, each approach has its strengths and trade-offs. In this post, we’ll explore three popular battery thermal management systems; air, liquid & immersion cooling, and where each one fits best within battery pack design.
Here’s a breakdown of the pros, cons and ESS recommendations.
Air-Cooling
Air cooling is the simplest and most cost-effective thermal management approach for battery systems. It typically uses forced airflow, generated by fans, to dissipate heat from the battery pack. As it doesn’t require a liquid coolant, pumps or plumbing, air cooling offers a lightweight and compact solution that’s easy to integrate, especially in smaller EVs, hybrids, or stationary battery storage systems. Additionally, there’s no risk of fluid leakage, making it a lower-maintenance option with fewer failure points. This method is particularly attractive for applications where thermal loads are moderate and tight thermal uniformity isn’t critical.
However, air cooling has significant performance limitations. Its low heat transport capacity can lead to uneven temperature distribution across cells, which affects battery efficiency, degradation and overall safety. Managing airflow through carefully designed ducts and vents is critical, but even then, the system may struggle under high-load or fast-charging conditions. The need for additional heating systems (like PTC heaters or electric wires) in colder environments further complicates the setup. Despite its drawbacks, air cooling remains a viable solution when simplicity, low cost and ease of integration outweigh the need for high thermal precision.
Liquid cooling
Liquid cooling is one of the most widely adopted thermal management strategies for modern battery systems due to its excellent balance of performance and practicality. It uses a liquid coolant, typically a water-glycol mixture, that flows through channels or cold plates integrated within or around the battery pack. This method offers significantly higher heat transfer capacity compared to air cooling, resulting in more uniform cell temperatures, improved battery efficiency and extended lifespan. Its compact system design also allows for tighter packaging, which is ideal for applications where space is limited.
On the integration side, liquid cooling does require more complex infrastructure, including pumps, hoses, heat exchangers and fluid reservoirs. These components not only add cost and weight but also introduce the risk of fluid leakage and require regular maintenance. Additionally, in colder climates, the system may need integrated heaters to maintain battery temperature above minimum operating levels. Despite these challenges, liquid cooling has become the go-to solution for many manufacturers, especially when handling high charging rates, larger battery capacities or performance-oriented products.
Immersion cooling
Immersion cooling takes thermal management to a new level by submerging battery cells directly in a non-conductive dielectric fluid, allowing for maximum surface contact and heat transfer. This method eliminates the need for thermal interface materials (like thermal paste or pads). The result is an extremely efficient and uniform cooling, making it an ideal solution for high-performance applications that demand rapid heat removal, such as fast-charging systems, motorsport EVs or aerospace-grade battery designs. It also inherently limits the risk of thermal runaway, adding a critical safety layer.
Despite its advantages, immersion cooling is complex and expensive to implement. It requires careful fluid management, robust sealing and a sophisticated control system to handle the fluid dynamics and thermal regulation. The cost & weight of dielectric fluids along with their environmental impact (e.g., global warming potential or recyclability) can be significant drawbacks. Furthermore, even with immersion, a chiller is still needed to regulate the fluid’s temperature, adding to system complexity. That said, for cutting-edge applications where thermal stability and safety are non-negotiable, immersion cooling remains a highly effective and innovative solution.
ESS’s Thermal Design Philosophy
- Model early, test often: We use CFD tools to simulate air flow, pressure drop and coolant flow before any hardware is built
- Right-size the system: Overspecifying thermal solutions adds weight and cost, we design to match your real-world load profile
- Design for diagnostics: Temperature sensing and fail-safes should be built into the control strategy, not added later
Conclusion
I am afraid that there’s no one-size-fits-all solution. The right cooling approach depends on application demands, environmental constraints and pack architecture. At ESS, we help clients make informed thermal decisions from concept through validation, because cool packs are safe, robust and long-lasting. Contact us if you have any cooling system design/review requirements.