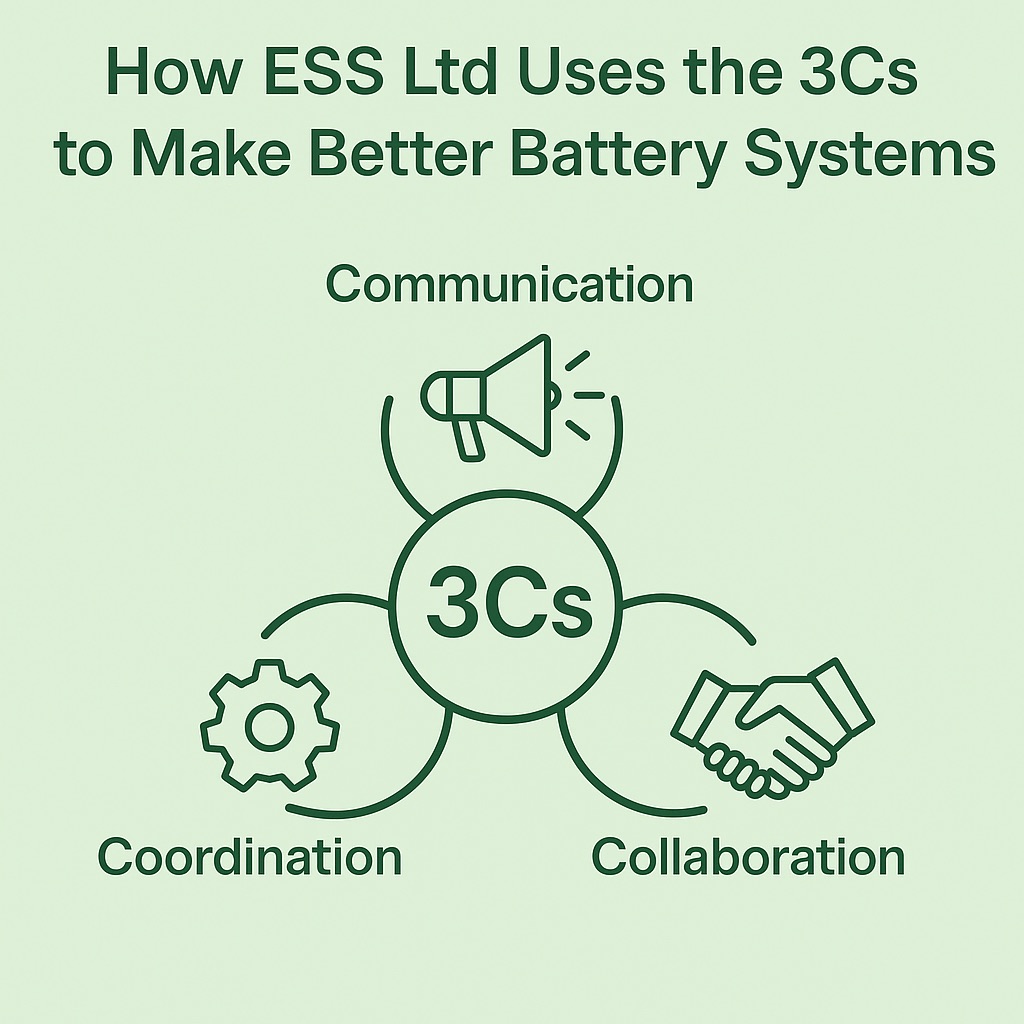
In today’s electrification landscape, building a safe, high-performance battery system isn’t just about chemistry or hardware — it’s about seamlessly integrating expertise across multiple engineering domains. At Energy Storage Specialists Ltd (ESS), cross-disciplinary collaboration is at the core of everything we do.
From strategy and cell selection to thermal management, mechanical integration, validation and manufacturing, ESS takes a holistic approach to battery engineering because delivering the right solution means more than just getting the specifications right. It means understanding how every part affects the system as a whole.
Why Cross-Disciplinary Thinking Matters in Battery Development
Battery systems don’t exist in isolation. They’re a tightly interwoven part of the broader product or platform whether it’s a high-performance electric vehicle, a renewable energy grid solution or an off-highway workhorse. A change in one area, like cell format, impacts others: cooling, packaging, BMS architecture, safety and even cost modelling.
Many of our clients come to ESS because they need a partner that understands not just one aspect, like thermal or mechanical design, but how all those elements interact and where trade-offs have to be made. That’s where our cross-functional team excels.
Here’s how we embed cross-disciplinary collaboration into every stage of the battery development lifecycle:
a. Strategy Meets Engineering Early
We combine market insight, technology forecasting, and deep engineering expertise to define the right product architecture from day one. This strategic foundation ensures that every design decision is grounded in real-world demands and commercial viability.
Key questions we ask up front:
- What does the end user need in terms of energy, power, weight, safety and lifecycle?
- What are the regulatory and certification requirements in target markets?
- What cell technologies and chemistries are emerging and are they production-ready?
- What’s the thermal and mechanical environment the system will operate in?
- How scalable/modular does the design need to be across platforms or applications?
- What suppliers and components can be brought into the design?
By answering these questions early, we ensure our battery system architecture is not only technically sound but also manufacturable, certifiable and market-ready.
b. System Engineering as the Glue
Our systems engineering team acts as the connective tissue, ensuring that electrical, mechanical, thermal and software disciplines work together cohesively. We use a model-based approach to define requirements, manage interfaces and identify risks early.
For example, when we size a pack, we’re not just considering cell energy density. We’re also:
- Mapping voltage windows to the powertrain or power conversion system (PCS)
- Developing mechanical layouts that withstand structural stresses from external forces, including crash loads and abusive mechanical scenarios.
- Balancing thermal loads with cooling system integration
- Aligning control strategies with the BMS and charger
The result? A system that performs as intended with fewer surprises during testing or integration.
c. Deep Dive Expertise in Each Discipline
While we take a holistic approach, we also bring deep domain expertise in the core areas that matter most:
- Thermal Design & CFD: We use simulation tools to optimise cooling strategies before a prototype is built
- Mechanical & Structural Engineering: From vibration fatigue to drop-test performance, we design for durability
- Electrical Architecture & BMS Integration: We specify busbar design, contactors, fusing and communication protocols
- Safety Engineering: We understand hazard mitigation, isolation monitoring and functional safety from the ground up
Each of these teams feeds into the same development roadmap — reducing rework and accelerating validation.
d. Testing With Purpose
Because we understand how subsystems interact, we design validation plans that matter. We don’t over-test or under-test, we test what counts e.g.:
- Real-world load profiles
- Thermal runaway propagation risk
- Structural integrity under shock & vibration
- Charge/discharge cycling with system-level metrics
Our ability to correlate data across domains gives clients confidence in real-world readiness.
e. Manufacturing in Mind From Day One
Cross-disciplinary thinking also means we consider design for manufacturing (DfM) early. We collaborate with suppliers and integrators to:
- Optimise module layouts for automation
- Select materials that balance cost, performance and sourcing risk
- Plan thermal and safety features around real-world assembly processes
This approach helps clients avoid late-stage redesigns — and gets them to market faster.
f. Where this approach pays off
We’ve applied this cross-disciplinary methodology to projects across sectors, from e-motorcycles to stationary grid storage. Here’s what it delivers:
- Higher reliability through tighter system integration
- Faster time to market via fewer development loops
- Better cost control with aligned trade-off decisions
- Stronger innovation through combined domain insight
Conclusion: Integration is Innovation
At ESS, we believe that the best battery systems aren’t built in silos, they’re built by cross-functional teams who understand how disciplines interact, complement and challenge one another.
It’s this systems-first mindset that allows us to deliver engineering solutions that are robust, scalable and ready for the real world.
Whether you’re an OEM with a bold new platform or an innovator tackling your first electrified product, contact us, ESS is here to help bring it all together, from concept to commissioning.
Leave a Reply