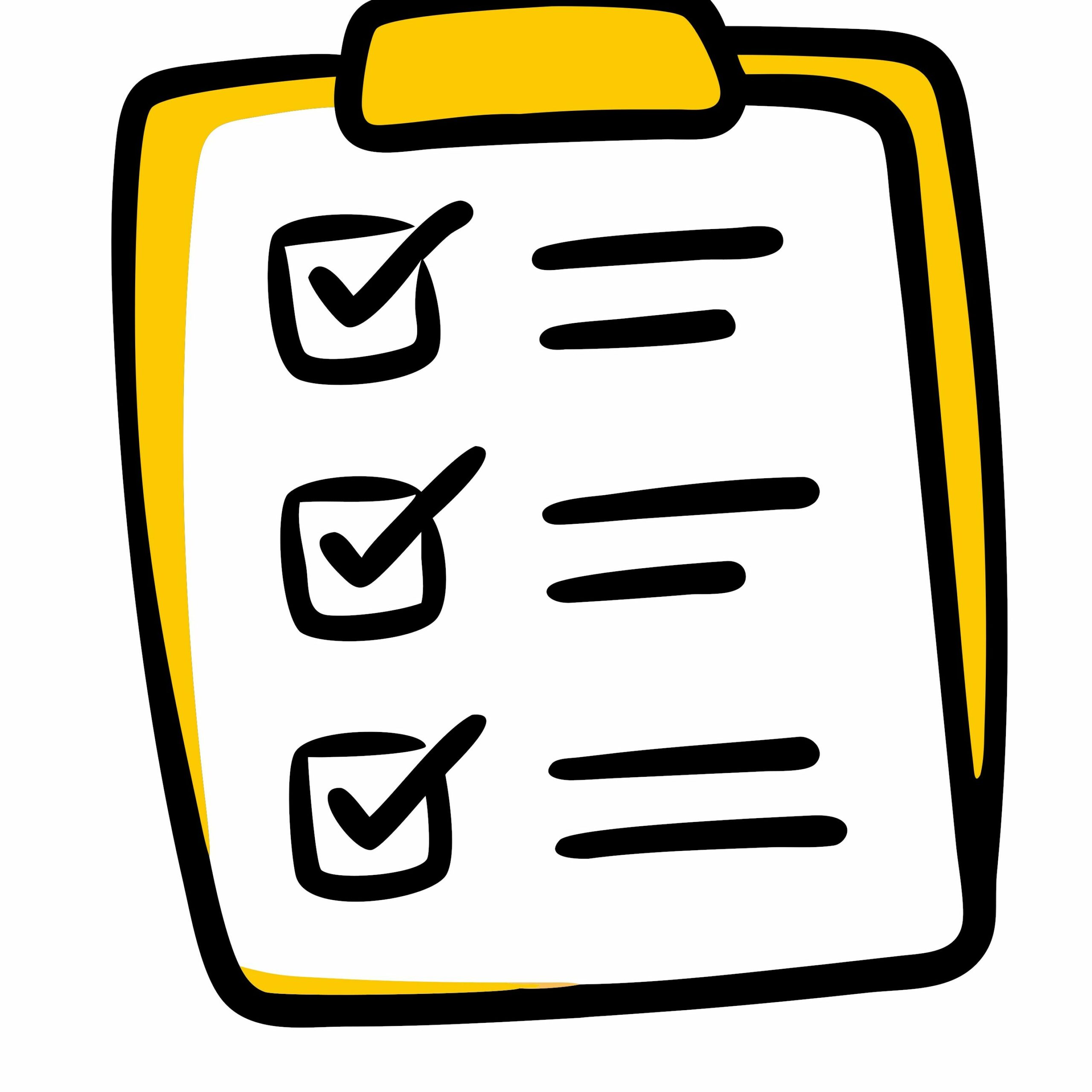
Designing a reliable, safe and efficient battery pack isn’t just about selecting the right cells or managing heat, it’s about integrating every subsystem into a cohesive, validated system. At Energy Storage Specialists Ltd (ESS), we’ve worked across sectors like e-mobility, marine, aerospace & grid storage and we’ve distilled that experience into a comprehensive battery pack design checklist.
Whether you’re building your first prototype or iterating on an existing design, this checklist helps you de-risk development, avoid late-stage surprises and move faster to market.
1. Define the Use Case & Load Profile
Before any CAD is opened or cells are sourced, clarity on the mission is key:
- What is the daily energy demand?
- What are the peak power and duration requirements?
- Will the pack face high vibration, salt spray or altitude extremes?
- How often will it charge? Fast or overnight?
- What are the regulatory and safety expectations?
This step shapes every decision downstream from chemistry choice to mechanical protection.
2. Cell Selection
Cells are the foundation of your pack, so selecting the right one is crucial:
- Should you go cylindrical, prismatic or pouch?
- Is high energy density more important than peak power?
- How stable is the supplier’s production and roadmap?
- What are the trade-offs in cycle life, thermal behaviour and cost?
Having navigated this data landscape before, we’re in a strong position to support your next steps
3. Electrical Architecture
A smart electrical layout is about more than volts and amps:
- Define series-parallel configuration based on energy and power targets
- Plan for fuse strategy, contactor specifications and pre-charge circuits
- Align pack voltage with inverter, PCS or motor controller requirements
- Anticipate protection requirements (e.g., overvoltage, isolation & short-circuit)
Robust electrical design lays the groundwork for system integration and functional safety.
4. Mechanical Design
Don’t underestimate how real-world forces can impact reliability:
- Use Finite Element Analysis (FEA) to simulate crash loads and stress concentrations
- Design for vibration resistance, especially for off-road, aerospace and marine applications
- Consider ingress protection (IP rating) against dust and water
- Prioritise serviceability, modularity and manufacturability
We model mechanical interactions from day one to minimise surprises during prototyping.
5. Thermal Management
Temperature is one of the biggest risks to battery safety and performance:
- Select the right approach: air, liquid or hybrid cooling
- Use CFD simulations to identify hotspots and validate designs
- Design for both thermal control and thermal runaway mitigation
- Balance cost and complexity against thermal performance needs
Every use case has different thermal sensitivities, we model for the worst-case, not the average.
6. BMS Integration
The Battery Management System is the brain of your pack:
- Ensure the BMS aligns with the pack’s sensing, protection and communication requirements
- Choose CAN, LIN, or Ethernet depending on the platform architecture
- Integrate State of Charge (SOC), State of Health (SOH) and balancing logic early
- Consider cybersecurity, redundancy and over-the-air (OTA) capabilities if needed
We tailor BMS integration to the project’s goals from off-the-shelf to custom firmware development.
7. Safety & Functional Testing
Test early, test often, and test for the real world:
- Conduct failure mode analysis and inject faults into hardware and software
- Evaluate thermal runaway propagation risk in worst-case scenarios
- Run shock and vibration testing in line with standards (e.g. UN 38.3 and OEMs own requirements)
- Capture data to validate your system, not just your components
Our validation plans align with the use case avoiding both over-testing and under-testing.
8. Manufacturing & Certification Readiness
A good prototype is just the start, the pack has to scale:
- Plan for DfM (Design for Manufacturing) and DfA (Design for Assembly)
- Ensure traceability of cells, components and critical process steps
- Align with relevant standards: IEC 62619, ISO 26262, DNV, etc.
- Build in quality assurance systems and test points into the design
We engage with suppliers and certification bodies early to streamline compliance and production
9. Lifecycle & Degradation Modelling
Model battery ageing over time to predict performance, optimise lifespan and plan for reuse or responsible end-of-life strategies:
- Simulate cycle life under real-world load profiles
- Account for calendar ageing, depth of discharge and temperature effects
- Integrate degradation models into system performance forecasts
- Plan for second-life applications or end-of-life disposal
10. Software & Controls Strategy
Design the pack architecture to support multiple configurations or future upgrades with minimal redesign:
- Define control loops for charging, balancing, thermal logic and fault response
- Ensure the BMS software architecture is modular and scalable
- Use Hardware-in-the-Loop (HiL) and Model-in-the-Loop (MiL) testing
- Incorporate diagnostics, logging, and OTA update capabilities if needed
Build a flexible, future-ready software foundation that enables advanced control, diagnostics and upgradability.
11. EMC/EMI Compliance
Design for electromagnetic compatibility from the start to avoid interference issues:
- Ensure design meets Electromagnetic Compatibility standards for your sector (e.g., CISPR 25 for automotive)
- Perform pre-compliance testing during early development
- Design proper shielding, grounding, and routing of HV/LV circuits
Prevent costly rework and certification delays by engineering electromagnetic compatibility into the design from day one.
12. Redundancy & Fail-Safe Strategies
Build in critical safety nets to prevent system failure:
- Identify single points of failure and introduce redundancy where critical (e.g., dual contactors, redundant voltage sense lines)
- Ensure graceful degradation or isolation of failed modules
- Align with functional safety frameworks like ISO 26262 or IEC 61508
Designing with fault tolerance in mind ensures the system remains safe and functional even when something goes wrong
13. User Interface & Diagnostics
Make the battery system transparent and service-friendly:
- Define SOC/SOH reporting, alert thresholds and user-facing indicators
- Provide external interfaces for service teams or operators
- Log data that supports root cause analysis and predictive maintenance
Making the battery system transparent and easy to monitor empowers users, operators and service teams alike
14. Pack-Level Modularity & Scalability
Design packs that can evolve with your product portfolio:
- Design modules that can be reused or stacked across different platforms
- Standardise mechanical and electrical interfaces where possible
- Make sure control logic adapts to pack scaling (e.g., parallel packs for large energy systems)
A modular design approach unlocks product flexibility, simplifies upgrades and reduces time-to-market across platforms.
15. Environmental & Sustainability Considerations
Future-proof your battery pack with greener design choices:
- Use materials and adhesives that support recyclability
- Assess carbon footprint of key components (cells, busbars, plastics)
- Consider compliance with regulations like RoHS and REACH
- Plan for pack disassembly or second-life use
Prioritising sustainability not only supports compliance, it adds long-term value through recyclability and second-life potential.
Ready to Build Smarter?
At ESS, we go beyond the checklist, we work alongside you to adapt it to your unique project needs. Whether you’re developing an e-motorcycle pack, engineering for offshore renewables or scaling up grid storage, our cross-functional team brings strategy, safety and system performance together from day one.
Contact us to find out how we can support your success.
Leave a Reply