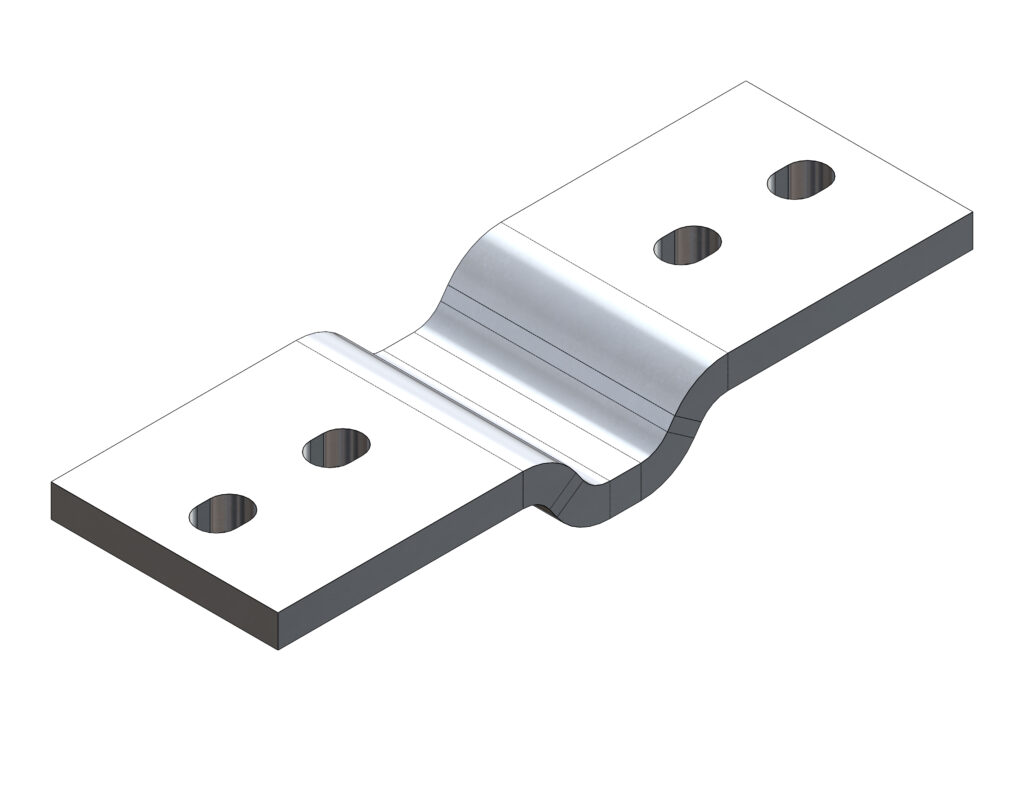
Imagine, you are developing a module for a large BESS system which is composed of 12 Li-ion packs of 20 modules of 20 cells each (assuming no parallel cell connections). The BESS system produces 3000 A continuously for 2 h so each pack produces 250 A for 2 h, do you use copper or aluminium for the cell-to-cell interconnect?
Below is part of the process that I’d go through to come to a design selection. So let’s get started and go through several parameters which will hopefully help us reach a suitable technical decision
1. Bus bar maximum temperature
Firstly, let’s agree on a maximum bus bar temperature which should not be exceeded. As we are working on a BESS system and that it is important for Li-ion cell to not be exposed to high temperatures, we shall limit the cell-to-cell interconnect temperature to 55 oC.
2. Cross section area discussion
Due to the low temperature limit, typical rule of thumbs are of no use, so the only way forward is to use a model. You are in luck because I have developed a quick Excel model to provide a good approximation on that I use in concept studies. This model says that the cross section area must be at least 135 mm2 (27 x 5 mm) and 175 mm2 (35 x 5 mm) for copper and aluminium, respectively.
Copper is a definite winner if you are designing for extremely tight space. This would be even more obvious as current increases. However, should we stop here?
3. Weight discussion
Let’s assume a bus bar length of 60 mm, which gives us a material volume of 8.1 cm3 and 10.5 cm3 for copper and aluminium, respectively. With density of 8.96 g/cm3 for copper and 2.70 g/cm3 for aluminium, the cell to cell interconnect would weigh 72.6 g and 28.4 g. That’s a 2.5 times weight saving for aluminium.
In our example, there are 20 cells so 21 cell-to-cell interconnects per module. This grows to 420 units per pack and 5,040 units per systems. In terms of weight, assuming the cell-to-cell interconnects only, 365.9 kg of copper vs. 143.1 kg of aluminium. This is a 222.8 kg savings on cell-to cell interconnects only!
Aluminium is a clear winner when it comes to weight savings for the same current density. This would be even more obvious as current increases.
4. Manufacturing discussion
One important step in Li-ion module production is the connection of the cell-to-cell interconnect to the cell tabs. This has different approaches: a) welding (laser most likely) and b) manual assembly.
Laser welding is widely used in battery module manufacturing due to its high precision, fast processing speeds, ability to join dissimilar materials and ease of automation. However, it also comes with challenges, including high initial capital expenditure (CapEx), ongoing maintenance costs, safety concerns and the need for careful joint preparation.
The introduction of green lasers is improving weld quality, energy efficiency, and sustainability, especially in applications involving copper, which absorbs green wavelengths more effectively. This results in lower energy requirements and more consistent welds. For aluminium, however, blue lasers are generally more effective due to better absorption characteristics.
In contrast, the manual approach is the simplest and most cost-effective, with minimal CapEx and low maintenance requirements. It’s easy to implement during the engineering phase and poses less risk to production continuity. Should a manual tools fail, they are inexpensive and easy to replace (e.g., a torque wrench vs. a laser welder). The trade-off is a longer takt time and less scalability. Manual assembly may not be suited for all applications like EVs but for non-moving systems, it could be use depending on the production number requirements.
Overall, there are no real differences between the 2 metals when it comes to production.
5. Cost
The typical cost is 9 $/kg and 2.5 $/kg for copper and aluminium respectively. Using the calculations we made previously that yielded to 365.9 kg of copper and 143.1 kg of aluminium, the savings would be $2,935.35 on the cell-to-cell interconnect alone!
If you are cost driven and your use case is not that stringent that you could use aluminium, a significant cost savings could be achieved
6. Thermal transfer
When it comes to power loss, copper dissipates around 7 W of heat (the above length of 60 mm and cross section is assumed), while aluminium releases approximately 15 W, more than 2× higher. This makes aluminium less thermally efficient, meaning it may require a more robust thermal management strategy to keep the system within safe operating temperatures.
The higher the C-rate the more likely copper is to be used, so it is important to consider the usage case of the application as using copper could add unnecessary BoM cost as discussed previously.
7. Recycling and environmental impact
Finally, it is important to consider recycling and environmental impact aspect of the metals. Both copper and aluminium are highly recyclable, making them environmentally favourable materials for use in Li-ion battery modules. Copper retains nearly 100 % of its conductivity even after multiple recycling cycles and recycling it uses up to 85–90 % less energy than primary production, significantly reducing CO2 emissions. However, mining and refining copper are resource-intensive and can have serious environmental impacts if not managed properly.
Aluminium is also extremely recyclable, with the recycling process requiring only about 5 % of the energy used for primary smelting. It is lightweight, which contributes to overall energy efficiency in electric vehicles. That said, primary aluminium production has a high carbon footprint due to the energy-intensive electrolysis process, often powered by fossil fuels. Therefore, increasing the use of recycled aluminium in battery modules can greatly reduce environmental impact and support circular economy goals.
Conclusion
In conclusion, while the development of the cell-to-cell interconnect may seem straightforward at first, it requires careful consideration and a few key criteria before making the right choice. If you need assistance with your battery development project, feel free to reach out. I have the expertise and resources to help you navigate the complexities and challenges throughout the development process.